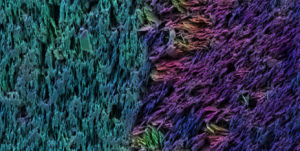
Querschnitt des künstlichen Zahns unter dem Elektronenmikroskop (Falschfarbenbild): Im Zahnschmelz sind Keramikplättchen vertikal angeordnet, im Zahnbein schräg bis horizontal. © Hortense Le Ferrand/ETH Zürich
ETH-Materialforschende entwickeln ein Verfahren, mit dem sie die komplexe Feinstruktur von biologischen Verbundmaterialien wie Zähnen oder Muschelschalen nachahmen. Sie können damit künstlich Materialien erschaffen, die genauso hart oder zäh sind wie ihre natürlichen Vorbilder.
In der Natur gibt es kaum langlebigere und zähere Strukturen als Zähne oder Muschelschalen. Das Geheimnis dieser Materialien ist ihre besondere Feinstruktur: Sie sind aus verschiedenen Lagen aufgebaut, in denen unzählige Mikroplättchen in jeweils identischer Ausrichtung aneinander gefügt sind.
Zwar gibt es bereits Methoden, mit denen Materialforscher Perlmutt imitieren konnten. Nach wie vor aber war es eine Herausforderung, ein Material zu erschaffen, das die gesamte Muschelschale nachahmt und vergleichbare Eigenschaften und die komplexe Struktur erreicht.
Nun hat eine Gruppe von Forschenden um André Studart, Professor für komplexe Materialien, ein neues Verfahren entwickelt, welches das natürliche Vorbild beinahe perfekt imitiert. So konnten die Wissenschaftler ein mehrschichtiges, zähes Material herstellen, das auf dem Bauprinzip von Zähnen oder Muschelschalen beruht und den Vergleich damit nicht zu scheuen braucht. Den ETH-Forschenden ist es erstmals gelungen, in einem einzigen Stück verschiedene Lagen mit unterschiedlich orientierten Mikroplättchen zu erhalten.
Ihr Verfahren nannten die ETH-Forschenden «magnetisch unterstützten Schlickerguss» (englisch: Magnetically assisted slip casting, MASC). «Das Schöne an unserem neuen Verfahren ist, dass es auf einer 100-jährigen Technik aufbaut und diese mit moderner Materialforschung kombiniert», sagt Studarts Doktorand Tobias Niebel, Mitautor einer Studie, die soeben in der Fachzeitschrift «Nature Materials» erschienen ist.
100 Jahre alte Technik neu genutzt
Und so funktioniert MASC: Erst erstellen die Forscher von einem beliebigen Objekt einen Gipsabdruck, der als Gussform dient. In diese Form gießen sie eine Suspension, die magnetisierte Keramikplättchen wie zum Beispiel Aluminiumoxid-Plättchen enthält. Die Poren der Gipsform saugen den flüssigen Anteil der Suspension langsam auf. Dadurch verfestigt sich das Material von außen nach innen und wird hart.
Einen schichtartigen Aufbau erhalten die Wissenschaftler, indem sie während des Gussvorgangs ein Magnetfeld anlegen, dessen Richtung sie in regelmäßigen Zeitabständen ändern. Solange das Material flüssig ist, richten sich die Keramikplättchen am Magnetfeld aus. Im verfestigten Material behalten die Plättchen ihre Orientierung bei.
Über die Zusammensetzung der Suspension und die Ausrichtung der Plättchen lassen sich über einen fortlaufenden Prozess in ein und demselben Objekt verschiedene Schichten mit unterschiedlichen Materialeigenschaften erzeugen. Dadurch entstehen komplexe Materialien, die natürliche Vorbilder wie Perlmutt oder Zahnschmelz nahezu perfekt imitieren. «Unsere Technik ist ähnlich wie 3D-Printing, jedoch zehnmal schneller und viel kostengünstiger», sagt Florian Bouville, Postdoc bei Studart und Co-Erstautor der Studie.
Künstlicher Zahn aus der Gipsform
Um das Potenzial der MASC-Technik aufzuzeigen, fertigte die Forschungsgruppe von André Studart einen künstlichen Zahn an, dessen Mikrostruktur diejenige eines echten Zahns imitiert. Die Oberfläche dieses Kunstzahns ist hart und komplex strukturiert wie diejenige eines echten Zahnes, während die darunter liegende Schicht weicher ist, genau wie das Zahnbein im natürlichen Vorbild.
Erst stellten die Erstautorin der Studie, die Doktorandin Hortense Le Ferrand, und ihre Kollegen einen Gipsabdruck eines menschlichen Weisheitszahnes her. Diese Gussform befüllten sie mit einer Suspension, die neben Aluminiumoxid-Plättchen auch Glas-Nanopartikel als Mörtel enthielt. Mit einem Magneten richteten sie die Plättchen senkrecht zur Oberfläche ihres Objektes aus. Nachdem die erste Lage trocken war, gossen die Wissenschaftler eine zweite Suspension in dieselbe Gussform. Diese Suspension enthielt jedoch keine Glaspartikel. Die Aluminiumoxid-Plättchen in der zweiten Schicht wurden mithilfe des Magneten waagrecht zur Zahnoberfläche ausgerichtet.
Diese zweilagige Struktur wurde schließlich bei 1600 Grad «gebrannt», um das Material zu verdichten und zu härten. Fachleute sprechen bei diesem Vorgang von Sintern. Zuletzt füllten die Forscher die Poren, die nach dem Sintern noch vorhanden waren, mit einem in der Zahnmedizin verwendeten Kunststoff-Monomer, welches sich anschließend polymerisierte.
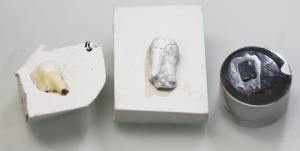
Das natürliche Vorbild in der Gipsform (l.), das Imitat aus dem neuartigen Verbundmaterial, das bereits gesintert wurde, sowie ein in einen Sockel eingepasster Kunstzahn, der für die Elektronenmikroskopie mit Platin beschichtet wurde. © Tobias Niebel/ETH Zürich
Kunstzahn verhält sich wie echter Zahn
Mit dem Resultat sind die ETH-Forscher sehr zufrieden. «Das für den Kunstzahn erhobene Profil für Härte und Zähigkeit deckt sich genau mit demjenigen eines natürlichen Zahnes », freut sich Studart. Das Verfahren und das daraus hervorgehende Material würden sich daher für die Zahnmedizin anbieten.
Die aktuelle Studie sei jedoch erst ein Machbarkeitsnachweis, der aufzeige, dass sich die natürliche Feinstruktur eines Zahnes im Labor nachbilden lasse, so Studart. «Damit man das Material als Zahnersatz verwenden kann, muss man jedoch dessen Aussehen stark optimieren.» Der künstliche Zahn zeige allerdings deutlich auf, dass man mit dem neuen Verfahren ein Mass an Kontrolle über die Mikrostruktur eines Verbundmaterials erreichen könne, die bislang lebenden Organismen vorbehalten blieb. Ein Teil des MASC-Prozesses, nämlich die Magnetisierung und Ausrichtung der Keramikplättchen mithilfe des Magneten, wurde bereits patentiert.
Das neue Fertigungsverfahren für solch biomimetischen Komplexmaterialien lässt sich jedoch auch anderweitig verwenden. So könnten anstelle der Aluminumoxid-Plättchen auch Kupferplättchen verwendet werden, was den Einsatz solcher Materialien in der Elektronik zuließe. «Ausgangsstoffe und Orientierung der Plättchen lassen sich beliebig kombinieren, sodass rasch und einfach eine große Palette verschiedenster Materialtypen mit unterschiedlichen Eigenschaften realisierbar wären», sagt Studart.
von Peter Rüegg, ETH Zürich, 28.09.2015
Originalpublikation:
Le Ferrand H, Bouville F, Niebel TP, Studart AR. Magnetically assisted slip casting of bioinspired heterogeneous composites. Nature Materials, AOP, 20th Sept 2015. DOI: 10.1038/nmat4419